Red Brick Community Project
The story so far
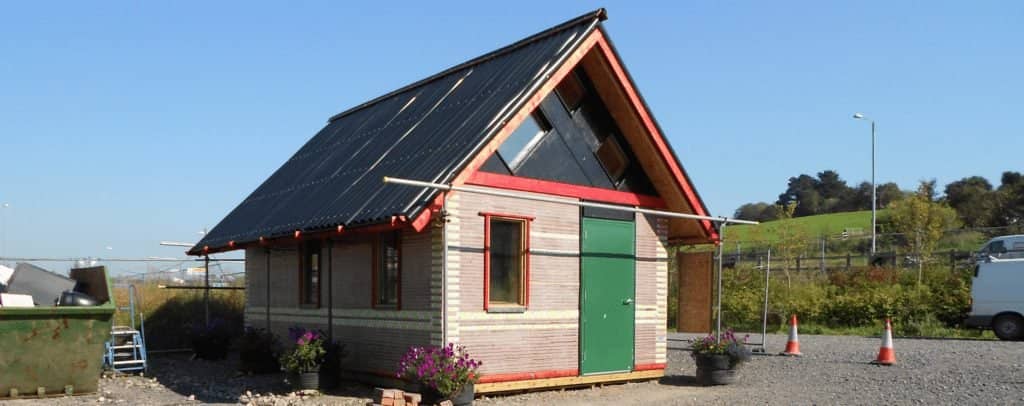
Above is the visitor office that we built at the project. It is made out of 5000 Argos catalogues, a mile of old guttering, some pallets and other stuff, by us, and grannies, and children.
This video is a great record by Neil Clarke who was there in the early days and who followed the whole project. You will be able to find more video contributions by Neil and other people on YouTube.
If you want to know where the project is now and everything that is going on, and how to be part of it, go to the Red Brick Building website, or better still go down and find out.
This page is a personal one about my involvement with the Red Brick Project.
The Red Brick Building Project on the old Morlands Sheepskin Site in Glastonbury
I was not around for the beginnings of the Red Brick Project, and had not the vaguest idea what it was about when I first tripped over it. It was January 2011 and bloody freezing.
I was having a bit of a mosey round to see if I could find a site in full public view where I could build an experimental affordable house without planning permission in order to draw attention to the problem and upset as much of the establishment as possible.
Affordable housing was what I had decided to spend my time doing when I retired, but renovating our local Burtle Village Hall with straw bales, mud and sheep fleece had sort of held me up for eighteen months. But now I was back on track. Or so I thought.
As I drove past the old Morlands site I saw a large banner and a bonfire. The banner said something about a red brick building and Ecos Trust and please buy a share. I had met Charles Couzens at Ecos Trust and was trying to get into their good books to help me lobby the Clarks to set up an affordable housing project, so I popped in.
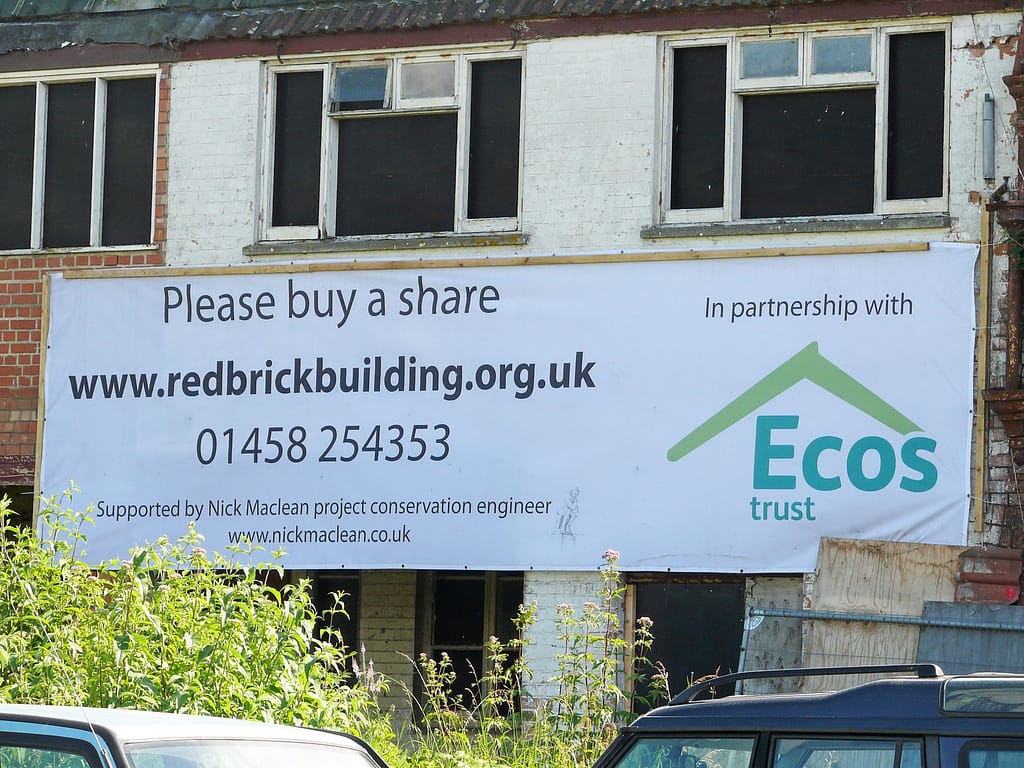
They were in the middle of a massive clear up trying to get the building secure and watertight by March 31st because SWERDA had said that if they did, the project could have the whole Red Brick Building Site, freehold and free for a pound!
SWERDA are, or were, the South West of England Regional Development Agency, now shot by the coalition government for being a spectacular waste of our money. The Regional Development Agency was a Quango set up by the Blair government in 1998 to encourage and stimulate Urban Regeneration. Not a bad idea in principle, but a very silly idea if you are going to put career civil servants in charge of it. They acquired the whole site in around 2000 and in the next ten years managed to waste a good deal of £20 million of our money on clearing it, cleaning it up a bit, and organising some traffic lights. This was on the totally daft concept that cutting edge IT companies would flock to buy the individual sites and put up iconic buildings on them. Then they would do cutting edge IT stuff with cutting edge IT staff presumably recruited from amongst the sheep farmers of the Somerset Bogs. To nobody’s surprise except SWERDA’s it didn’t happen.
£20 million and a decade of work resulted in the arrival of Screwfix! Not that there is anything wrong with Screwfix, but it isn’t exactly cutting edge.
There were a couple of buildings on the site they couldn’t knock down because they were listed, and they had presided over the renovation of a row of listed cottages which are now useful homes. Joe lived in one of them. As I became more involved in the project I developed a short story to tell people who visited how it had all come about. It involves quite a lot of poetic licence and may not even be entirely true but nobody has questioned the general story, so here it is, as I often told it.
Up until the seventies the two big employers in the area were Clarks shoes in Street and Morlands sheepskin in Glastonbury. In fact Morlands began before Clarks when a couple of Clark brothers began making slippers from sheepskin off-cuts. In the seventies Morlands got it spectacularly wrong by over expanding and opening posh shops in places like London, Paris, and New York at precisely the time that sheepskin was going out of fashion, and went bust. Two thousand direct and indirect jobs were lost and the site became derelict. At the same time Clarks got it pretty much right by recognising that the best way to make money was by branding and marketing, rather than by making shoes. The result was that its Street factories became Clarks Village but another two thousand jobs were lost.
SWERDA had nearly completed the destruction of the rest of the Morlands site when a group of the predominantly young, and, from what I am told, Chris Black, occupied the Red Brick Buildings in the freezing cold of the winter of 2008. As I understand it, they were asking that those buildings be retained and developed to provide facilities and opportunities for the young. In the end SWERDA agreed that they would give the buildings to “The Community” provided it could put up a sensible proposal for using them since as far as SWERDA were concerned the only plan that added up was to knock them down like everything else that wasn’t listed.
By this time the young and cuddly, having done the cold and uncomfortable bit had largely melted away to get on with their lives, and making a case for the project became the job of the great and the good.
Sarah and Paul Sander-Jackson, who had an impressive track record from the St Werburg’s City Farm and the Riverside Garden Centre Coop in Bristol, together with Ecos Trust and Alan Gloak were the backbone of setting up the vehicle that was to become Red Brick Building Centre Ltd. This was a Community Benefit Society in which shares could be purchased so that “The Community” would own the project; there would be a limit to the size of any one shareholding and in any case a shareholder would only get one vote irrespective of the number of shares held. This sounded OK to me.
Paul was certainly the brains behind the legal structure as the vehicle for this community vision. Sarah seemed to be single-handedly responsible for pulling in significant finance and influential investors, much of it with a level of sheer enthusiasm which those individuals obviously found difficult to resist. As the project CEO she seemed to be an adrenalin fuelled tour de force. During those early weeks she would appear on site like a small tornado, often with a prospective someone important in tow, and, almost invariably having temporarily lost or forgotten her mobile phone, car keys, hand bag, computer, singly or all of them, and sometimes more than once a day each. However, if I suggested something half sensible I wanted to do, and was prepared to get on with it, she almost always agreed to it instantly, which endeared her to me within hours of meeting her. She agreed to the scrap scheme on the spot, and then to the Argos Office because I could raise the minimal funding to do it through the scrap scheme.
Anyway, when I turned up on the Monday with enough tools to help get the building watertight with the rest of the volunteers, Chris Black had just been fired. This was, apparently, because he had been doing what Chris Black wanted, as opposed to what he was being asked to do. This meant that being fired had little effect on what he was doing, which he carried on doing anyway. It subsequently became apparent that expecting Chris to anything other than what he wanted to do was the result of a touching level of naivety in some, but by no means all members of the project.
I had enough to keep me busy which was just as well because I am not good at working outside in the perishing cold, especially if I don’t even have to do it to make a living. Despite the fact that I really wanted them to be pleased with me, and to be impressed with them, at the end of the first week my impressions were pretty dire.
I gathered that Ecos Homes were the commercial wing of Ecos Trust. They had successfully renovated some old buildings at Great Bow Wharf in Langport, where they had also built some very interesting houses which I had visited. They had just completed some high quality sustainable houses in Stawell, and their plans for Red Brick were that they were going to set up a sustainable building centre and provide training and consultancy in sustainable building techniques. And yet, for me the first week had “piss up” and “brewery” written all over it. The job was being managed on site by someone who seemed to have no experience of how to run, manage, or look after a bunch of volunteers, and seemed to prefer not really to be seen in the open air at all. The foreman was affable and experienced but I really think would have been happier working on agricultural buildings, and certainly not having to look after a bunch of obviously anarchic volunteers. I had agreed to volunteer specifically providing that I wasn’t putting anyone out of work who needed to earn a living. Within a few days the paid chippy was told to go and find something else to do. The water froze almost every night, and the generator regularly ran out of fuel, both due to complete incompetence and bad organisation. At the end of each day what tools there were, were chucked into a container in a heap. If you wanted anything you would have to trample over a pile of stuff and untangle whatever you wanted. The whole job was a mess.
And then, at the end of the week the wages didn’t turn up. Until this point I hadn’t realised the volunteers were being paid. In fact the only people doing stuff who weren’t being paid turned out to be me and Chris Black. And he wasn’t being paid because he’d been sacked!
On any building site on the planet, wages not turning up is as good as an instruction to look for another job. There are only three reasons why wages are late. The firm is in financial trouble: it is fundamentally incompetent, or it really doesn’t care that much about its workers. There are no other excuses, and all three are usually terminal for the firm concerned. I went home pretty depressed at the end of the first week. My problem was that I didn’t want to believe what that first week was telling me because I thought the project was a great concept.
At the end of January I wrote to Charles Couzens. This is the first paragraph.
January 29th 2011
Dear Charles,
I have enjoyed working on the Red Brick project over the last couple of weeks and hope my help made a worthwhile contribution. Would you be kind enough to thank Chris and Nathan for their help and support? I would be very interested in becoming more involved with the design and construction aspect of the project if you feel I may have useful ideas and experience to offer. Of course I would get involved in the physical work as well. However, I am not really interested in just “going back to work,” especially if I am not even going to be paid!
I suppose I shouldn’t be surprised that I didn’t even get a reply. I got the impression that they thought they were the experts and my help wasn’t needed. However, since I still felt the project was worth supporting, I decided to make my contribution in a different way. I didn’t exactly chuck my teddy out of the pram, but I did decide that I didn’t want to become involved in the main renovation since it didn’t look as if it was going to be tackled in a way I would enjoy anyway. So that is how it came about that we got a scrap scheme, a visitor office made out of Argos Catalogues, and Stuart’s café.
The deal with SWERDA was that the buildings had to be watertight and secure, and I think we had undertaken to raise a certain amount of money by way of a Community Share Issue which ended on March 31st 2011. SWERDA would then hand the site over to us, work could begin and Buildings A and B and were scheduled to be completed in October 2011.
Community shares were £100 each, and although there was a fantastic amount of goodwill towards RBB because something useful was finally happening on the old Morlands site, £100 seemed quite a lot to me. So I set up the scrap metal scheme. The idea was that if you hadn’t got £100 for a share you could still help the project by giving us any old metal you had. It was on the principle of the widows mite. We acquired a little old caravan from Ecos which Chris Black kindly delivered. It was still very cold so that little caravan became a refuge all day every day for the next six weeks. We got the necessary Environment Agency licences in record time. Thomas’s the Glastonbury scrap metal merchants agreed to provide us with a skip, and we opened on Feb 17th in 2011.
On the following day Joe appeared. Joe lived in the row of cottages at the other end of the site, but clearly regarded the whole area as part of his territory. Rather like a resident cat, nothing happens in his territory that isn’t checked out within hours. And so Joe came to see what was going on. From then until now he has been an indispensable and valuable support to me and the project. At thirteen he demonstrated a level of competence and maturity that impressed me and everyone he met. Joe would be a very good argument for kids being able to leave school before sixteen. I gather he was a bit of a pain at school and yet I always found him to be incredibly responsible and reliable. He has been one of the highlights of my time at Red Brick. Of course, every now and then he would do something daft, and you just had to remind yourself that he was very young for the responsibilities he often took.
He is, however, a bit of a magpie. He has a bit of a thing about bollards, barriers, Heras security fencing, construction signs of all kinds, and seems to regard them as “available” if left unattended, and out in the open. Unsurprisingly, this has led to him accumulating an impressive stock, each item labelled at least with his initials if not actually marked with urine.
In the days after we opened for business, BBC Somerset, Glastonbury FM radio, and the Central Somerset Gazette kindly gave us great publicity, and stuff started coming in. Not only did people bring scrap but working tools and stuff that wasn’t broken which we sold very cheaply. We also got tools we could send to Tools For Self Reliance which Dennis Massey’s team could send to Africa. Thomas’s, the Glastonbury Scrap firm provided us with skips, advised us and gave us money for everything we took in. In the six weeks that we ran it initially we raised about £2500.00 for RBB.
But money wasn’t the only thing that the scrap scheme brought us. It brought people on to the site so they could see what we were doing and got them involved which was great. At the time the RBB office was in the High Street. The scrap scheme convinced me that we needed a project office on site, and so that was how the principle of the Argos Office came about.
It’s not that I never do the same thing twice but I do like to try new things, and there didn’t seem much point in building a little visitor office if it wasn’t going to be a bit of an experiment and fun.
People do ask me how I think up these things to build and make them work. The basic answer is this. It helps to be quite old and have done a lot of different things, most of which inevitably didn’t work. You hang on to the few that did. This gives the impression that you know what you are doing. The next thing is that if you understand the principles of structure you can make almost anything out of anything. Finally, I had no formal training and I am not much of a craftsman. This meant that I had to design everything I wanted to do down to my ability to make it which was pretty rudimentary. It turns out that this was a very good discipline and has helped me to do things that involve volunteers and grannies and children because if I can do it anyone can.
So I had done straw bales on the Burtle Village Hall, which meant thinking of something else, and this meant some kind of “brick”. I wanted a brick that everyone would be familiar with, and preferably could get hold of so that they could bring one. This had worked very well at Burtle where we used 4000 wine bottles as cavity wall insulation in the base of the straw bale walls. They weren’t ideal cavity wall insulation but they were free, they didn’t rot and everyone could bring one, and they did. In weeks we had to go on the radio to turn them off!
Yellow pages came to mind so I wrote to them and asked if they would help. They replied threatening to sue me if I even considered it, since, they pompously told me, they had spent forty years developing the “Brand Image” of Yellow Pages and they weren’t about to have forty years of “Branding” undone by some idiot making a building out of them on a main road where everyone could see it, without it costing them a bean! In fact it was just as well because Yellow pages are all different thicknesses and the important thing about bricks is that they are uniform unit size. But I did write and tell them what a boring bunch of plonkers they were.
So the next thought was Argos catalogues which were a better idea anyway. They were easily available and everyone knew what they were. However, I would need around 5000 of them and whilst I knew people would bring them I also knew they wouldn’t manage 5000. It was now March, and Argos had a new issue coming out in July so I set about trying to get hold of what they might have left over.
Argos is a big company. I can’t tell you how many departments they have, each of whom thought that this request might be the responsibility of one of the others, or any of them that wasn’t the one you were talking to. They have a Press Office and a Media Relations Department. They have a Department that deals with Charities and one for Corporate Social Responsibility. These are in addition to the separate Departments for Advertising, Marketing, and Public Relations. That is seven. I was hoping that I could persuade them to ship their leftover copies down to their depot on the M5 at Bridgwater and then get them to us. But it was now May and they still didn’t seem to know which department would deal with it.
Eventually, I got a somewhat stuffy letter saying No. The gist of it was that their Health and Safety people had looked at it and decided that walls built by some lunatic out of Argos catalogues might fall over and squidge an unreasonable number of children. Even if they weren’t liable for squidged children it wouldn’t look good on the PR front, so sorry but No! This was a bit of a blow, had it not been for Nick Maclean. Nick is an extraordinary structural engineer with an international reputation, and had been the engineer for the RBB since the beginning. He has been involved in saving a number of important, but otherwise condemned buildings, and coming up with innovative methods for repairing them.
At this stage of the Argos design I planned to wrap the whole building in film to protect the catalogues from the weather. In fact it didn’t work and we did something else, but at the time it enabled Nick to save the little project for me. He wrote to Argos explaining that the building was to be wrapped in the same stuff they used for wrapping bricks on pallets which were then put on lorries and driven round roundabouts without any falling off at all. As an eminent engineer he was quite satisfied that no children were likely to be squidged. It did the trick. They wrote to me saying that they would deliver the fifteen tons of leftover catalogues to Bridgwater. However, that was the extent of their involvement. It was our problem to get them to Glastonbury. They could offer us no publicity or other help, and would not wish to be further involved. I didn’t care. I had got what I wanted so we could finish the job. This was just as well since I had already designed the entire thing in my head based on using them. Of course, all the actual staff we met in Argos were amazed that Head Office was so uninterested in what they and the rest of us saw as a great publicity gift but there you are.
Alan Gloak said it was like Boots and the sheep. Glastonbury has the right to drive a flock of sheep up or down the High Street, for a reason I don’t know.
This is a right that those involved exercise on an annual basis. On a recent occasion some sheep had gone AWOL and went to have a look in Boots before rejoining the procession. Since it was a public occasion there was plenty of video and some good pictures of the whole event, in which Boots expressed a profound indifference. They could almost certainly have got some great “here come the girls” publicity, but either those who work in that department were too stupid to recognise a gift when they saw it, or perhaps each department in the “customer facing” role in Boots thought it was the job of one of the others.
As it turned out Sparks Transport very kindly picked up the catalogues and delivered them to us, and we managed perfectly well without any further involvement of Argos, but I still think it is a shame they didn’t join in a bit.
Alan Gloak is the Chairman of RBB, and the most delightful anachronism. I don’t know why I think of him as out of his time but he does seem to represent a way of life and a set of values that we somehow lost most of by the end of the Second World War and what vestiges might have remained were extinguished by the selfish greed of the Thatcher years. He has the avuncular confidence of a lifetime devoted to the public good and knowing how the public good works. He was one of the few who turned up often, even when he didn’t have to, and nothing much was happening, just to see how it was all going. I had to avoid mentioning anything we might need, for fear that Alan would instantly offer to pay for it out of his own pocket.
The scrap scheme was meant to be a temporary project until the end of the share issue but it wouldn’t lie down. People just kept bringing stuff so we set it up again and kept it running until September 2013 when we didn’t really have the capacity to run it properly. I have now bought the container and moved the scheme up to the Paddington Farm Trust where we hope to give it a new lease of life for that project.
By May 2011 we had got the building but nothing much was going on down “their end”. Up our end we had the scrap scheme, I started building the Argos Office and towards the end of the month Stuart came. Stuart Constable was running the catering for 700 people at Thales in Wells, but they were shutting the site down. I don’t know how Sarah S-J found Stuart but she did. We had decided that in addition to having the project office on site it would be good if we could set up a small café. This would attract people to visit the project, feed the workers and the volunteers, and hopefully enable whoever ran it to eventually move into Building A where a café had always been part of the plan.
Stuart agreed to come and give us some advice and maybe lend us a bit of kit, which belonged to him. He did not want to run it himself let alone get involved in anything like a burger van. Within days he had gone out and bought one, got it on site, spent all hours getting it up and going, moved in and ran it with virtually no time off at all, through a freezing winter until October 2012 when he moved into Building A a year after Plan One said it would be ready. I know that during that time he did not even manage to scrape a living. I also know that we would not have managed without him. Sarah Bewley had worked with him at Thales and without her help and support he would not have had any time off site at all. By the end of June we had built a small covered seating area, and later in the year we filled in a bit more, but that was it. For a couple of months it seemed as if the Argos office, the scrap scheme and the cafe were more or less all that was going on.
In June we were visited by Andrew Tweedie who took some great pictures from a van with a telescopic pole with a camera attached to it.
This next section is specifically about building the Argos Visitor Centre, so you could miss this section out if you jusy want to know about the Red Brick story as I saw it.
How to build a Visitor Office out of Argos Catalogues.
I always mean to take more photos than I do. At the very beginning there was nobody around so I can’t find many photos. This is why I have had to put in some terrible sketches of what I did. Almost all the photos about building the little office were taken by Neil Clarke or Patsy and Robert Atkins.
We had a good hardcore base, which wasn’t far off level so it was fairly easy to put in a pallet plinth. Second hand pallets are a fantastic resource, BUT BUT BUT….if you are going to use them whole for floors or walls for example THEY MUST ALL BE EXACTLY THE SAME SIZE. You can use one size for the floor and a different size for walls of course, and then use all the odd ones for furniture or individual items. BUT, if you try to make a base out of mixed sizes it won’t work and you will just get frustrated and cross. In this photo the black stuff is old plastic guttering that I am already collecting for the roof, which is an idea I think I invented, but I expect someone will tell me I didn’t.
I explained to everyone that I had decided to build the roof first because then we could make the rest of it without being rained on, and that the safest place to build a roof was on the ground, so that is what we did. While I got on with making the roof, Abbey Scaffolding put me up some cunning scaffolding which I had designed and which Nick Maclean had given his blessing. The tyres were to become planters with flowers in them. Since some of this scaffolding was destined to become part of the finished building, the flowers and tyres would save me from having to wrap each pole in red and white fuck off tape in order to stop stupid people from bumping into them.
As I have said in my diagram, the roof is made of twelve identical boxes. Each pair is set up at right angles and joined up as you can see. I wrapped each box in silage wrap which is very cheap but kept the rain off while they were exposed to the weather.
I needed one person to help me with moving each box which was fine when Stuart arrived, but we had to wait until we had got four people to move each “A” section over beside the building so we could “tile” it. The tiling consisted entirely of recycled plastic half round guttering laid in any lengths as long as you lap them so the rain runs off. It is exactly the same principle as Roman pantiles still used universally in the South of France. If the Romans had had Osma plastics, they certainly wouldn’t have bothered to make clay pantiles! In fact I had a bit of a result with the guttering because while I was trawling the plastics recycling businesses I came across a huge load which one of the manufacturers had rejected and sent for recycling. They let me have it provided I didn’t tell anyone where it came from, and I never did know what was supposed to be wrong with it. It saved me a lot of scrounging from the fascia and gutter guys because I think we used over a mile of it, but in theory you could collect as much as you needed for any size roof.
One of the cunning advantages of my design was that if you do the sums right you can arrange to have a “cup” at the edge of each section which means that when we had got the roof on all we had to do was to “cap” each join for a perfect weathertight seal.
By the time the guttering was on, four of us could still move each section on the ground, but there was no way we would be able to lift them on to the roof. I always knew this and had planned to ask Snows to help us. They had been very generous in giving us some materials and doing us a good deal with the rest but they didn’t agree to lift the sections on until the last minute, so it was a great relief when they did.
The picture above is a detail of how the “A” sections sat on the two parallel scaffolding bars. Although this was a very simple and structurally sound way of doing it, it did depend on the “A” frames being pretty accurately made and the scaffolding bars being exactly right as well.
Although the principle of everything that I do is that it should be extremely simple, sometimes it does have to be accurate as well. My rule is that everything has to be “good enough”. Sometimes a couple of inches in any direction is good enough, but sometimes it has to be within 5mm or it won’t work. One of the Burtle farmers who helped with the Burtle Village Hall Project said that usually the nearest field was accurate enough for the stuff he did!
With all six sections on all we had to do was bolt them together, and cap each join with guttering to have a perfect roof. It was up and watertight in under three hours.
It was now June 29th 2011 and I think we had just got the agreement of Argos to let us have the catalogues and get them down to the Bridgwater warehouse. I can’t remember exactly when they came but we were building with them by the beginning of August. This means that we built the the walls and windows and everything during July. What I mainly remember is that I wouldn’t have managed to complete the structure without Thomas Sander-Jackson and Alex. However, I don’t seem to have many pictures of either it or them. I suppose it might be that I meant to take pictures and didn’t as usual, and perhaps the photographers were on holiday or had lives to get on with!
In fact, building the room under the roof was a piece of cake since the main structure was already sound so the walls didn’t really have to do much except keep the wind out. However the pictures above and below do show a couple of things. I made the walls with a space for the door but without any windows. This is because all the windows were based on free recycled double glazing units usually thrown in the skip when windows are replaced. Tons of these are thrown away every week. However, you can’t make the window frames until you know the exact size of the window and you don’t know that until you have them. So, you build the walls and cut the window holes afterwards. I will give you some more details on these great free windows a little later.
The other thing I needed to worry about was the plinth that the catalogues were going to sit on, which needed to be exactly the right width all round. So, I could cut the windows in wherever I wanted but the plinth for the ” bricks” had to be millimetre accurate. Part of the reason for this is quite boring but crucially important. If you look very carefully you will see that the pale green floor very slightly overhangs the pallet base and the plinth in turn overhangs the floor. The plinth is 10mm ish narrower than an Argos catalogue, so that the bottom course of catalogues just hangs over the edge. This means that all rain drips off everything without being caught and soaking in. If you are going to make a building out of what is fundamentally paper, sawdust and wood shavings, and you don’t understand this you will finish up with a soggy pile of something pretty mushy.
This principle is at the heart of nearly every construction. Wherever water can be trapped and hang around it will rot wood. If the building is metal sooner or later it will corrode or rust. If it is concrete, when it freezes it will blow it apart. If you understand this and a bit of geometry you can make almost anything!
This is probably a good time time to do windows. I got the original idea from Caroline Barry’s straw bale house and The Garnet Ghost Town in Wyoming ( or was it Montana?). I reckon I improved it a bit with the cill and the hose pipe and draught excluder but the principle is not original. OK, this is how you do it. You get your window units for nothing and work out how big a box you need to allow about 10mm all round with some extra at the bottom to make a sloping cill, with a bit of lead fkashing sandwiched to run the water off. What we did was to get the width right, with the sides a bit longer than you need. Then you put the sloping cill in and stand the glass unit on a bit of half inch garden hose which acts as a squashy bottom seal and a hinge. This will tell you how high the box should be. Its depth should be so that it protrudes through the wall exactly the width of an Argos catalogue! We made the frame inside the box with roof batten off cuts and put adhesive draught excluder on it. This means that when you shut the window there really are no draughts and the wedges hold it shut. With a bar on a screw at the top it is now as secure as any window in your own house. Once you have a window box the right size, hold it against the wall where you would like a window, draw round it, and cut out the hole. Simples! Here are another couple of pictures of windows in the finished job. If you still can’t work out exactly how to do it, contact me.
Sparks transport picked up about twenty pallets of redundant catalogues weighing about fifteen tons and we stored them in the corridor of Building C.
There are lots of pictures of everyone building with catalogues on the website and Neil Clarke’s video. We had a couple of Argos catalogue building weekends for Grannies and children which I think everyone enjoyed a lot. The children drew pictures and wrote messages and put them in the catalogues before gluing them in with PVA, which is OK for children to use because they use it even in playgroup. In fact the catalogues were not really holding the building up because the roof was already supported by the scaffolding skeleton. It was just a question of stacking them on the plinth and sticking them neatly against the outside “wall”.
Except of course that it wasn’t quite that simple, because it never is. With a conventional book the spine is slightly thicker because of the stitching and folding. This means that if you stack them all the same way round too high they fall over. This seemed not to be true with the catalogues, which appeared to lie quite flat on the pallets all the same way round. So we just started building with the cut side out because the coloured sections looked prettier. However by about three foot up our walls were beginning to get a bit slopy and I was worried that they were going to pull off the wall and slide out so we reversed them. The problem got instantly worse and we realised that the water in the PVA glue was swelling them slightlyat the back. Putting the cut edge in first made the swelling worse. So I rushed home and got some spare 5″ feather edge fencing. This is the old fashioned wedge shaped fencing stuff that you usually nail on vertically and each bit overlaps the next. From then on we slipped a bit of that in every few courses and it worked a treat.
The other thing was half bricks! If you are going to have to go round corners and build round windows and up to door frames, you don’t just need half bricks. You may need to “tailor” bricks. And a bolster and lump hammer won’t do it! Just to save you the trouble in case you ever decide to build something out of catalogues or books, hand saws, jig saws, band saws, chop saws etc don’t work. What worked was a printer’s very expensive guillotine. The only reason that Walton Press agreed to do it for us at all was that we provided them with a pristine pallet of catalogues in which we could guarantee no metal ( like staples for example.) The practical problem for me was that I wanted to build over the weekends and Walton Press quite reasonably wanted to go home on Fridays. I did a lot of homework on very careful measuring and got all the specials precut. I then threatened everyone with instant death if they used the wrong bits in the wrong places and apart from the odd glitch that only I ever notice it went pretty well.
Building the walls went pretty well, and by half way through September we were ready to wrap! It seemed like a good idea but it didn’t work. The film didn’t “cling” to the catalogues, rather obscured the surprisingly crisp look of the whole thing, and just looked a bit of a mess. This is another important rule of things like this. If something doesn’t work as well as you had hoped, and you have done your best to solve any problems, and you still don’t like the result, dump it. Find a better way to deal with it rather than trying to make what turns out to be a bad idea work.
So, we “pointed” the gaps and varnished the building. I don’t like compromising with materials so I planned to use clear Dow Corning anti fungal silicone for the gaps and Pacific Mega which is a water based floor varnish. However, both of them are very expensive. For much less than half the price we used Proper Job clear silicone and Screwfix No Nonsense floor varnish.
The wheelchair access ramp is another idea I think I sort of invented and brought from other projects I have done. You make a flat grid of bricks on edge. then you cut up anything you like into slices around 50 mm wide. In this case we mainly used pantiles and double and triple roman roof tiles but you could use slate, plastic guttering, ceramic tiles, waste pipe, all of which I have used elsewhere. Then you fill a square with a 3 : 1 dry mix of sand and cement. Use a lump of 4 x 2 longer than the grid as a “tamper” and make whatever patterns you like in the square, tamping it down flat as you go. When you are happy with the result, make sure your pattern is full of dry mix and very gently water it with a watering can with a fine rose. You might have to top up, but if you are careful the water will wash your pattern and the weather will harden off the whole thing in a few days. Sliced roof tiles won’t last forever because eventually the frost will get in and crumble them, but I have got areas ten years old which still look fine.
It is now November 2013 and it is about to face its third winter. A week ago Joe gave it a brush down and another coat of Screwfix No Nonsense floor varnish. It seems to be fine. It is dry as a bone, and snug as a bug.
I totally forgot to mention money.
Quite a lot of the materials were free, thanks to a lot of people but especially Snows Timber. Some were free anyway, like the old guttering, the window units and the fridge packing insulation. However, if we had paid for everything that we needed, including wiring it up to give us light and power, it would have cost about £1500.00. Since this gave us about 250 square feet of useful space it works out at about £6.00 per square foot. For another £1000.00 we could have made it Building Regs compliant, which means that you could live in it. We had a queue of people who would have happily lived in it. This would mean that it would cost about £10.00 a square foot or around £100.00 a square metre. Depending on who you talk to, domestic building costs are between £800.00 and £1400.00 per square metre. This is around a 90% saving compared with one of the big, greedy builders.
A mortgage on my Argos house would cost about £25.00 a month!
I am not suggesting for a moment that it is sensible to build houses out of Argos catalogues but it makes you think doesn’t it. If you want to know what else I think about affordable housing, have a look on that page.
So, now back to the Red Brick Story…..
So here we are in June 2011. To be honest I can’t really remember exactly how the falling out with Ecos happened, but it was all fairly fraught. Costs were escalating and remarkably little seemed to be happening. There were already a lot of reasons why Ecos were a complete waste of space so far as I was concerned, but that was OK because I had announced that I was quite happy in what I called the playground so it wasn’t my problem. In any case I was obviously a complete menace on a proper building site because of Health and Safety. Health and Safety as a major industry had not been invented when I began, and other than being careful and responsible it is still a bit of a mystery to me. I have never had a certificate which officially says that I have learned not to fall off a ladder. Anyway, by the time that the office, and the rest room, and the wet room, and the drying area, and loos and a lot of signs designating PPE areas arrived I was quite glad that I was safe in the playground. In addition, most of what would be regarded as risky operations in the building of the Argos office were over before officialdom was likely to spot me doing them.
Certainly Sarah had decided that it just wasn’t working with Ecos and set about firing them, and, as it turned out, did a pretty good job.It had always seemed a bit odd to me that they apparently owned 50% of the whole building without having invested a penny. Orme Architects stepped into the breach, and Don Stratton took the role of Site Manager, with a brief to hit the job and get it done. Sarah, who had been absolutely crucial to getting the funding and driving the project so far, found herself increasingly out of her zone in charge of a building project. By Christmas costs were obviously out of control and Don called a halt to work until we could sort out where we were.
The Vision for Building C
A few things had been going on in the meantime. Tom Clark had proposed that we set up an anarchic little group, not officially anything at all, to think about the grand future of the project and in particular Building C. This consisted of Tom and Mike and Gareth and me. The plan for A and B was that they should be offices, studios, meeting rooms and the cafe, and that once up and running would help to finance work on C which was half as big again and more expensive to deal with. We ruled out retail on the basis of location, performance because of parking and the Arts generally since in funding terms it would be very hard in the current economic climate, and unlikely to be a commercial proposition.
We already reckoned that Building C was not much of a commercial proposition anyway, and that it was unlikely that Buildings A and B would be able to subsidise it.
The most promising area was education and training which seemed to be pretty much what the vision for the project was. In other words to promote the “making of things” and the provision of the training in craft skills and entrepreneurship which would provide the area’s young with the skills and opportunities so desperately needed.
I dredged up the bones of a project I had originally proposed to the newly independent Zimbabwe, in the early eighties, when Mugabe was still regarded as a good guy. Because of its history as a very paternalistic colony the newly emergent state was desperately short of skilled and managerially trained people who weren’t white. I had proposed setting up “Enterprise Colleges” by taking over or setting up major commercial undertakings in mining, engineering and food processing, all of which were already well established industries, and mostly foreign owned. The unique thing about these “Enterprise Colleges” was that whilst they were to be fully commercial operations, the profit priority would be sacrificed for training and developing skills so that black Zimbabweans would be fast tracked to be able to run these businesses. I had got on very well with my contacts at the Zimbabwe High Commission in the Strand, but it suddenly went cold and no-one would talk to me so I had to abandon it.
The Vision for Building C, was a grand concept which was roughly this.
That Building C should itself become a giant training exercise. We would gut the building and create a steel matrix inside it which would serve to stabilise the building and provide us with a modular framework within which the building could be renovated on an incremental basis using different building techniques. The students themselves would be involved in every aspect of the build including the administration, wages department, HR, stock control, purchasing etc. The plan was that although it was to be a construction project, students of all disciplines would benefit from the experience and confidence to be gained by being involved in the creation of a live building. As each unit was completed it would become available as a workshop or studio to a small business start up or one that would undertake to offer training.
By the end of 2011 I had sold the idea to Bridgwater College who offered construction courses and were very keen on the whole concept. We were also keen to involve Strode College and had a meeting with their top people at which they expressed not much interest in being involved at all.
By this time I had joined the board of RBB. When Don called a halt to work it was agreed that Don and I would sit down together and look at where we were. I agreed, but on the basis that if I was going to take real responsibility I needed paying, but minimum wage would do. Almost as soon as we looked at the figures it was obvious that we couldn’t afford me! We had no money, and avoided having to declare the whole project insolvent by around £3.50 and ten minutes.
It was agreed that the three major investors would put in £10K each and we would get A and B secure and watertight by the end of March. This would mean that we would be in a position to “mothball” the entire project if we had to. During this period Don and I would also produce a budget for what we reckoned it would cost to get A and B finished sufficiently to get up and running.
Tom Clark in particular, and the Glastonbury Trust made it fairly clear that they saw a firm committment by Bridgwater College as a condition of providing any further major funding. I suppose that this was really a key decision in the the future of the whole project. I knew that however keen Bridgwater College were, they were not going to invest hard cash even if they would be permitted to as an educational establishment. This meant that if Building C was going to happen we needed serious funding. My idea was that whilst BWC were going to be absolutely key to getting the money there was no point in them actually being on site until the “Vision for Building C” was a reality. However, the RBB investor’s club wanted a committment now, and it turned out that BWC was quite keen to set up a presence in Glastonbury, so that they could offer local courses, particularly in construction that Strode College didn’t offer anyway. My main contact at BWC was Elaine Morrissey, in the Business Development Unit. She absolutely “got” the whole concept and so did her boss, Andy Berry, who subsequently became Vice Principal. Matt Tudor took over as head of the BDU and he was also sold on the project. What we needed was a “Letter of Intent” from BWC saying that they were committed in principal to the long term and would take teaching space in building B. In fact Elaine Morrissey proposed that they move a teching Portacabin in in July and start straight away. We got the letter signed in early June, and Don and I started work again at the beginning of July. In fact, partly due to BWC health and safety jobsworths and general pratting about the portable teaching space never did turn up, and they didn’t actually sign a lease on their space until the following year.
However, so far as Don and I were concerned we had got money, we had a budget, and had promised the building would be available to let by Jan 1st 2013. And, just as importantly, we had now got Katherine.
Katherine started at the end of May 2012 and for the first time we had someone capable of controlling the whole administration of the project. She was an absolute Godsend from the moment she arrived and has become increasingly important as time has gone on. Chris Trwoga had persuaded her to come. Chris had been sort of seconded to RBB by the Glastonbury Trust and also turned out to be indispensable. Each of them has devoted an extraordinary amount of time and effort, most of which they weren’t being paid for at all.
Stuart and the cafe had endured a winter, and he was still at the heart of the project, physically, socially, and emotionally, but finding it an increasing struggle to make any kind of a sensible living. He had a number of factors working against him. He didn’t have any capital to put to setting up inside the building, and clearly wasn’t going to be in a position to pay the kind of rent that RBB was going to need to justify the space the cafe was planned to occupy. To be honest, he just isn’t an entrepreneur. He is a nice, kind chap who gave us all a lot of himself, but clearly wasn’t in a position to take the necessary gambles even if he had been able to see what they were. I realise that I am desperately searching for excuses for treating him pretty shabbily, and I am so relieved that he has now got a great job down at The Mill on the Brue where I think he will do a great job and I hope will be happy.
Mainly thanks to Don, we had done a pretty good job on the budget. The net result was that we got a lot more done than we had promised, we delivered on time, and inside the budget. To be honest it was a job that wasn’t that much fun for me. It was pretty much a rescue operation and trying to make a silk purse out of a pig’s ear. The investors chucked in money again, Alan Gloak single handedly fronted the cost for the kitchen, and Tom more or less totally funded the biomass boiler heating system whilst we had a couple of community share offers and did bugger all about promoting them! Tom got cross about Bridgwater College not moving in or putting up money even though I told him constantly that they weren’t going to and never were going to. However, they did put up some signs on the building which is one of the things I thought Tom wanted, but that managed to piss everyone off, and probably started the beginning of the end of the RBB project so far as I was concerned.
I had always been aware that involving Bridgwater College would be contentious, partly because it would poke Strode College in the eye, and partly because BWC were inextricably in bed with EDF who are building a nuclear power station. I didn’t care for two reasons. Firstly, Strode didn’t offer construction which I definitely needed, and were half asleep when we first tried to get them interested. In any case I had plans to get them involved in due course together with every other educational establishment in Somerset. Secondly, whilst building a nuclear power station may not seem to be very Glastonbury, I am afraid that the cuddly people of Glastonbury are a very small percentage of a population that was going to see its future for the next twenty years entwined with the biggest construction project in Europe, and the jobs that go with it. In any case, the whole green movement is riven by its attitude to Nuclear Power so it was a battle I was quite prepared to have. By the autumn of 2012 it was becoming increasingly apparent that Buildings A and B were going to be a reality. Somerset Arts weeks had happened, Stuart was in the cafe in a very simple form, and thanks largely to Katherine we had a stunningly successful open day at which we had over three thousand visitors.
There was now a concerted movement to “rescue” the Red Brick Project from Bridgwater College and the dreaded EDF by what I subsequently rudely called the Lalas. I must admit that I felt a bit like the little red hen. In the story the little red hen had found some seeds in the farmyard and decided to bake some bread. All the other animals in the farmyard seemed to be too busy to help her plant the corn, or water or weed it, and had other more important things to do when it came to harvesting, threshing or grinding it to make flour. They were curiously absent for the work of kneading and cooking, but all turned up to share the finished loaf. In the story the little red hen wouldn’t let them have any and she and her chicks ate the lot.
The “Vision for Building C” had been a fairly low key project that the shareholders were largely unaware of because we hadn’t told them about it! I was very keen that we get it out in the open in time for the AGM and confront the issue with the shareholders so that they could decide whether they approved of it despite its involvement of Bridgwater College. My colleagues on the board seemed keen not to have this discussion before we had a serious proposal to put to them. In a way this was fair enough since it is quite true that at this stage it was a brave and grand plan consisting entirely of smoke and mirrors. So there didn’t seem to be much point in prompting a massive discussion about something that might not happen at all. In the event they were probably right. However, since what was basically my plan for Building C was the only show in town they were happy for me to get on with it. Actually I don’t think most of the board were that keen to see it happen at all. Even at this stage I sensed that RBB was heading towards being a community arts project which is what some people had wanted it to be all along. This, and the fact that I was now too old and grumpy to dedicate unlimited time and effort to bashing my head against a brick wall, meant that I told everyone that I would hit it for three months and it was “shit or bust” as they say in polite circles. In fact I spent a bit longer than that but not much.
This is a summary of how we didn’t manage to get the Vision for Building C off the ground.
By December 2012 I had got considerable support from the Organisation running the Local Enterprise Partnership (LEP) and got agreement in principle to fund it provided that a feasibility study showed that it would stand up. The LEP was not able to fund a Feasibility Study.
By that time I also had the enthusiastic support of Tessa Munt and the full backing of Bridgwater College. I produced a request for a total of £80,000.00 to Vince Cable in the Department of Business Innovation and Skills with some optimism. Tessa Munt was a personal friend of Cable and worked for him. The proposal ticked every single box for the BIS and some they hadn’t even thought of, and the money involved was so piddling they could have done it out of petty cash! It also came with a time limit of the end of January for a decision. It was a very simple proposal which even a minister could understand!
The Red Brick Community Project Proposal (5)
By the end of January I had a reply via Tessa Munt that they were terribly short of money and despite wasting millions of pounds on IT projects that didn’t work were unable to find £40K for the first phase of this feasibility study whilst agreeing that it was just the sort of thing they supported! I was happy to declare “Game Over” and sod the lot of them. Tom Clark persuaded me not to, and Tessa insisted she could get Vince to come down, and she did.
In March I had a good meeting with the LEP who again insisted that they wanted to be involved together with Bridgwater College if we could fund the feasibility study and the project stood up. I decided that if I could get some official backing from BIS I would approach the RBB investors for the feasibilty funding.
On April 6th Vince Cable visited RBB. Matt Tudor (BWC), Sarah Sander Jackson and a few others got him on our own for half an hour or so and did a good job. He professed to very interested and supportive. However, any official backing would involve not only the BIS but also the Department for Education.
On May 14th 2013 Matt Tudor and I went to see Mat Hancock, Junior Minister for Education in Vince Cable’s department in Westminster. We began by saying that there was no point in patting us on the head and wishing us luck. We knew they weren’t going to produce any money but they did have to write to us endorsing the project, and agreeing to support our applications for funding to both the LEP and the EU. A couple of weeks later we got a letter patting us on the head and wishing us luck!. I sent a letter saying that, unusually in this case I would have preferred the poke in the eye with a stick since at least that would have shown some balls.
On this basis I simply wasn’t prepared to even consider asking the RBB investors to stump up for a feasibility study. So we were now at the end of May and this time I did call “Game Over”. I must say that surprisingly few people at RBB seemed to mind very much, so I am not sure they would have funded it anyway.
I was massively disappointed at failing to get the backing of Cable etc and it was a shame because those of us who worked on it thought it was a great concept. Since Building C was the one aspect of RBB that kept me involved, when it went my job was done. I wish the project every success. I hope the investors have got what they thought they were putting their money into, and that the project has become what the young and cuddly were freezing their bits off for in 2008.
Cheers RBB and Good Luck
Sent Dec 15th 2013
Dear All,
My useful contribution to the RBB is now done.
So this is the last newsletter you will get from me.
Most of you will know that I did not stand for re-election to the Board at November’s AGM.
Many of you will also know that my real interest in RBB was a plan we devised in 2011 to make Building C a giant training construction project, in which students of all disciplines from all Colleges would physically create the units that would become the workshops, studios, and business start ups that we felt were at the heart of the Red Brick Project’s vision from the very beginning.
Despite the support of Tessa Munt, a personal session with Vince Cable at RBB, and a joint visit with BridgwaterCollege to the Minister for Education at Westminster, we failed to get the support we needed to fund the initial feasibility study. We didn’t even ask them for money. We simply needed them to endorse the project and support our applications for funds. I am afraid that this is not the first time that I have found politicians in power to be a gutless, hollow, superficial, patronising bunch, who seem to have to agree to a lobotomy in exchange for a Ministerial Car.
I am really so sorry we failed. It is a great concept. I have attached the proposal I did for Vince Cable in December 2012 if you are interested. We kept it as simple as possible with lots of pictures so that even Ministers could understand it!
(We did ask for a possible £80K in that proposal, but said we would manage without it when they explained that they needed all the money so they could waste billions on IT projects that didn’t work!)
I am now playing (and hopefully helping) up at the Paddington Farm Trust. Next Spring we plan to build a classroom out of old pallets and other rubbish with the help of grannies and children and anyone else who wants to have fun.
In the meantime we have taken the scrap metal scheme up to PFT where we will recycle as much as we can and raise funds for PFT projects. Because we are less easy to get at, we will collect.
If you do want to know what I am doing, and how things are going, I am in the throes of setting up a web page.
There is a link at the bottom. If you “subscribe” to the Project Diary or the Blog I think it lets you know when I post something, but fails to let you know whether it is the least bit interesting.
Well, I think that is about it, except to wish you all a great Christmas and a Happy New Year.
So, if you have been, thanks for listening,
Robin
PS. For those of you who were totally confused by “So long, and thanks for all the fish”, here is the explanation which probably won’t help either.
So Long, and Thanks for All the Fish is the fourth book of the Hitchhiker’s Guide to the Galaxy “series” written by Douglas Adams. Its title is the message left by the dolphins when they departed Planet Earth just before it was demolished to make way for a hyperspace bypass, as described in The Hitchhiker’s Guide to the Galaxy.